电压:该模组有无过压与欠压、单个模组有无过压与欠压、模组之间电压是否平衡。
容值:是否满足电容最低容值(即最少满足风机1.5次安全收桨)。
常见的电容模组可靠性测试方案
通过充电器检测
原理:通过充电器充电检测超级电容模组电压,并计算超级电容模组容值。
方法:
充电器检测电容模组电压是否正常,检测所得电容电压应满足公式:Umin<U<Umax
Umin:超级电容模组最小允许电压(一般满足变桨电机1.5次收桨电压)。
Umax:超级电容模组最大允许电压(例如:不能超过额定电压10V)。
否则该电容模组电压异常。
根据公式: c1=I1×(t2-t1)/(U1-U2)得到超级电容模组在以I1=3A充电时的总容量,其中U1=80%UR,U2=40%UR,t1、t2充电过程中的时间点,UR为超级电容模组的额定电压。(见电容容值计算示意图)
根据公式: c2=I2×(t4-t3)/(U1-U2)得到超级电容模组在以I1=4A(该值不固定)放电时的总容量,其中U1=80%UR,U2=40%UR,t1、t2放电过程中的时间点,UR为超级电容模组的额定电压。
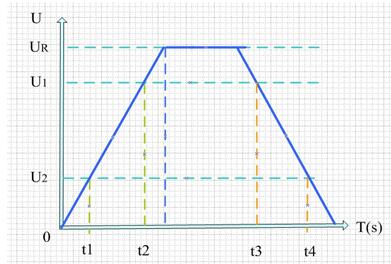
(电容容值计算示意图)
求两次以上不同电流的放电与多次充电计算所得超级电容模组容值平均值为:△C=(C1+C2+?)/n。
计算△C与该超级电容模组设计容值偏差系数,
应满足:
Pc= (△C)/C<20%
则该电容模组容值正常。
优点:充放电过程中容值测量较为精准.充电器能独立完成测试,操作过程简单,不需要变桨与主控制参与过多控制。
缺点:为保证风机正常运行,其过程中电容电压一直处于正常电压状态,很难实现完整的充放电过程,电压可能因充电检测回路或者通讯回路异常而测试不精准,同时容值也无法精确计算。即使完全实现上述过程风机也将较长时间停机无法操作,影响该风机的发电量。
通过电容检测模块检测
原理:超级电容模组供电回路增加霍尔传感器(即电流检测设备)用以检测该模组的充放电电流,通过电容监视模块检测该电容模组的电压,并计算超级电容模组容值。
方法:
电容监视模块检测电容模组电压是否正常,增加分电压检测回路。(即增加一个检测5个横组中的两个模组电压,见电压检测回路示意图)
检测所得的电容电压与分电压应满足公式:
Umin<U<Umax与
Umin×2/5<U1<Umax×2/5。
否则该电容模组电压异常。(2/5:分电压检测回路检测了2个模组的电压,其分压U1就应该满足总电压2/5U的各项指标。其增加了电容模组的电压平衡性检测。)
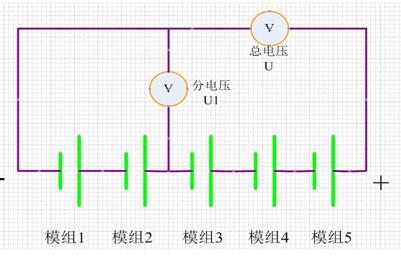
(电容电压检测回路示意图)
采集充放电时电流I.计算该超级电容的容值△C其计算的方法与使用充电器检测时的计算方法一致。
通过计算所得容值△C上传至变桨系统控制器,计算该超级电容模组设计容值偏差系数,应满足:
PC=(△C)/C<20%
则该电容模组容值正常。
优点:超级电容模组电压检测更为精确,同时还能检测该模组电压的平衡性,充放电过程中容值测量较为精准,对充电器要求比较低,也不需要变桨与主控制参与过多控制。
缺点:增加了检测设备(即增加了成本),同时与充电器检测方法缺点一样,风机在正常运行过程中其超级电容模组电压一直处于正常电压状态,很难实现完整的充放电过程,同时电压可能因电容监视模块检测回路或通讯回路异常而测试不精准,增加风机故障率,其容值也就无法精确计算。即使完全实现上述过程风机也将较长时间停机无法操作,影响该风机的发电量。
较新型的电容模组可靠性测试方案
原理:使用变桨驱动器给超级电容模组充电,并检测其电压与分电压。利用超级电容模组供电,用驱动器使用变桨电机进行收桨或开桨测试。通过变桨电机能量消耗计算超级电容模组容值。
方法(见流程图):
(1)通过变桨驱动器检测超级电容模组的电压与分电压,该方法与电容监视模块采集超级电容模组电压方法一样,检测所得的电容电压与分电压应该满足:
Umin<U<Umax与
Umin×2/5<U1<Umax×2/5。
否则该电容模组电压异常。
(2)通过风机主控选定该风机超级电容测试时间,其要求是每168小时一次(其时间间隔可以设定,以满足电容测试频率为佳),时间选定为9:00与17:00之间为宜(白天利于风机在测试过程中发现异常工作人员可以及时检修),且30秒平均风速应小于该风机最大测试风速(一般为8m/s,主要是为风机安全考虑)。满足测试条件后主控将变桨停机至限位,并给出电容测试开始指令。
(3)收到主控电容测试指令后,变桨控制“桨叶1”开桨到测试桨角(一般选择60°与70°之间,小于60°测试不通过可能影响风机安全,大于70°电容能量消耗少测试可能不精准),断开AC400V与驱动器的连接(通过自动控制接触器或者使用驱动器的半控桥断开AC400两种方法均可),使用超级电容模组供电让变桨电机以恒定速度(一般选择3°/s 与5°/s某一恒定速度)收桨到限位(92.5度)。
(4)记录“桨叶1”超级电容收桨前后电压差,
其计算公式:△Uact1=Ur1-Uact1,
Ur为收桨前超级电容模组电压,
Uact为收桨后超级电容模组电压。
其中△Uact1必须满足:(见电容电压差正常范围图)
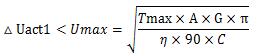
Umax:最大变化电压。
Tmax:电机最大力矩。
A:测试桨角。
G:变桨变比常数。
η:电机效率。
C:超级电容模组设计容值。
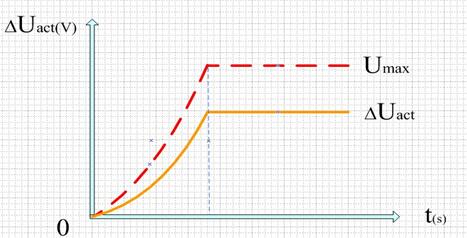
(电容电压差正常范围图)
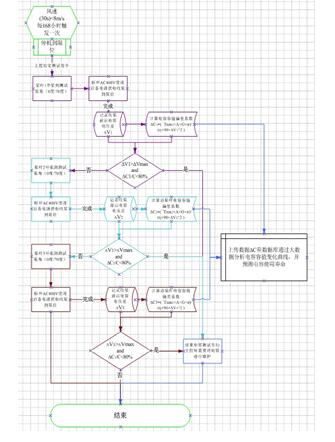
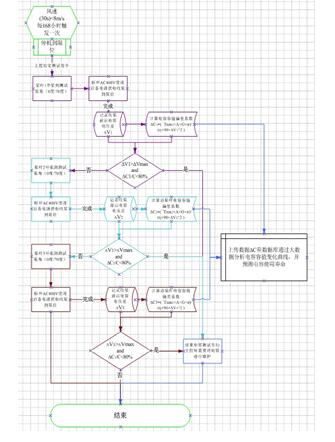
(控制流程图)
通过变桨控制器计算桨1超级电容变桨过程中电容的容值△C,其计算公式如下:
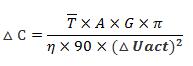
ˉT:该收桨或者开过程中的电机平均扭矩。
A:测试桨角。
G:变比常数。
η:电机效率。
计算超级电容模组设计容值偏差系数,应满足:
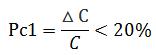
则该电容模组容值正常。
重复(3)、(4)、(5)步骤分别对桨叶2、桨叶3超级电容模组进行测试。其电压与容值均需要满足上述步骤内容。测试过程中某一桨叶的△Uact与Pc不满足运行条件,测试终至,恢复AC400V供电,并告知控制平台该风机超级电容模组需要维护或者需更换。
优点:减少了充电器和电容监视设备,节约了成本,其超级电容模组电压检测更为精确。通过驱动器就能判断应该超级电容模组能否满足风机安全需求。检测通过软件自动触发,无需要人工操作。检测时间选择多为无风期,同时检测周期短一次检测时间不超过180s,不影响风机发电量。该方案模拟了超级电容模组工作的真实情况,也能检测了超级电容模组的工作回路,提升了风机的安全与可靠性。
缺点:软件的可靠性要求要,同时对驱动器要求更高,驱动器的维护成本增加。该方案计算使用的电机效率是一个固定的理论值,那么计算所得的容值会有一定的偏差,但相对超级电容电压是额定电压状态时,利用充电器或电容监视器采集的超级电容容值更为精准。该方案联动性要求高,需要主控系统与变桨系统均对该方案 “出力”。
该方案的延伸用法:
风机的超级电容模组使用寿命大概在5年左右,那么就需要对风机的超级电容使用寿命做预测。利用该测试方案将每次超级电容模组测试完成后计算所得的△Uact与Pc上传至数据库。通过大数据分析超级电容模组的使用状况(其具体分析方法本文不做阐述),拟合出该模组容值衰老曲线,进一步可以预测超级电容的使用寿命,为业主对超级电容模组的使用与维护计划做更有利的安排。
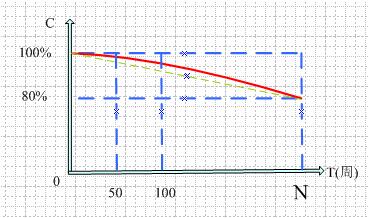
(模拟电容容值衰老曲线)
结语
做为风机的安全保障重要部分的超级电容模组,其可靠性要求非常高。那么风机运行过程中,电容模组的实时检测方法也就需要越来越可靠。无论是本文所提及的方案还是其它更好的方案我们都是本着风机的安全性与低故障率而考虑。也希望好的方案能在大型风电机组中应用,为绿色能源的有效利用做出贡献。
(作者单位:成都阜特科技股份有限公司)